Built around
Apollo is our primary AM platform, a modular system enabling flexibility and upgradability at ease.
Industrial-Grade Printing That Grows With You
Apollo Applications Across Industries
What Makes Apollo Different?
What’s in the Apollo System?
At the core of Apollo is the Rapid Fusion PE320 Pellet Extruder, designed for consistent high performance. It’s paired with our Epicurus Controller Pro, an open-source, customisable control system, alongside a KUKA robotic arm, Modular Heated Bed, Air Plus Kit, Smart Loom Pro, and pellet drying unit. Together, these components deliver seamless high-volume printing using raw thermoplastics. Whether integrated into a full production line or used independently, Apollo is your gateway to faster, cleaner, and smarter additive manufacturing.
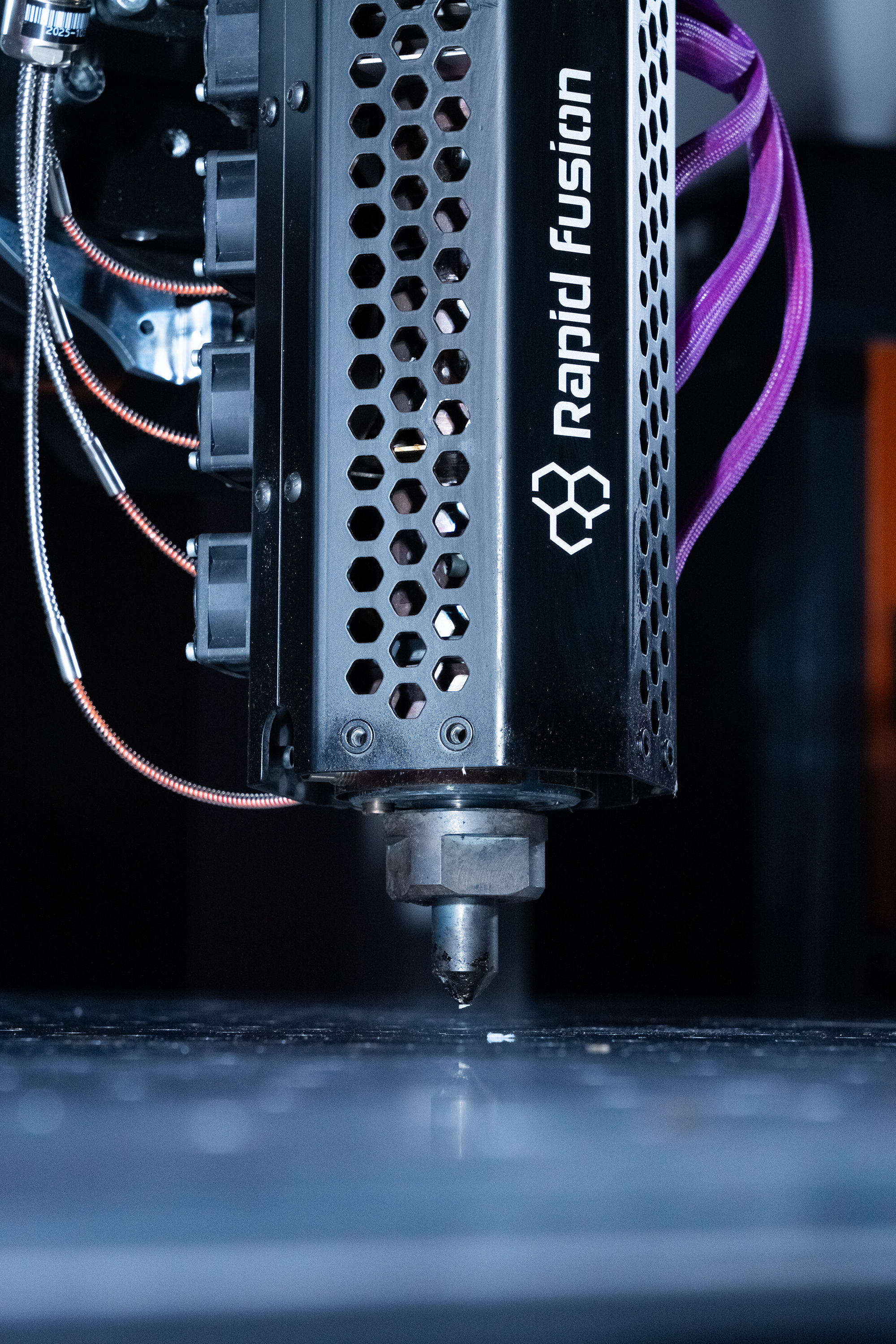
Rapid Fusion PE320 Pellet Extruder
The Rapid Fusion PE-320 Pellet Extruder is a versatile and powerful tool designed for industrial - grade 3D printing.
The extruder can reach temperatures up to 450°C, allowing you to work with a wide range of high-temperature materials.
Equipped with a robust Schneider motor, the motor provides Peak stall torque of 10.2 Nm and 8000 rpm speed, with a 1:25 Wittenstein German made gear box.
The extruder has four heating zones that enables precise temperature control, enabling optimal printing conditions for different materials.
It is designed to handle abrasive materials like carbon fibre, providing versatility in material options. Additionally, it can be used to upgrade a CNC machine or Robot to a 3D printer expanding the possibilities of your existing setup.
Use this text block to discuss some commonly asked questions like shipping and returns, sizing, warranties, or product and company details.
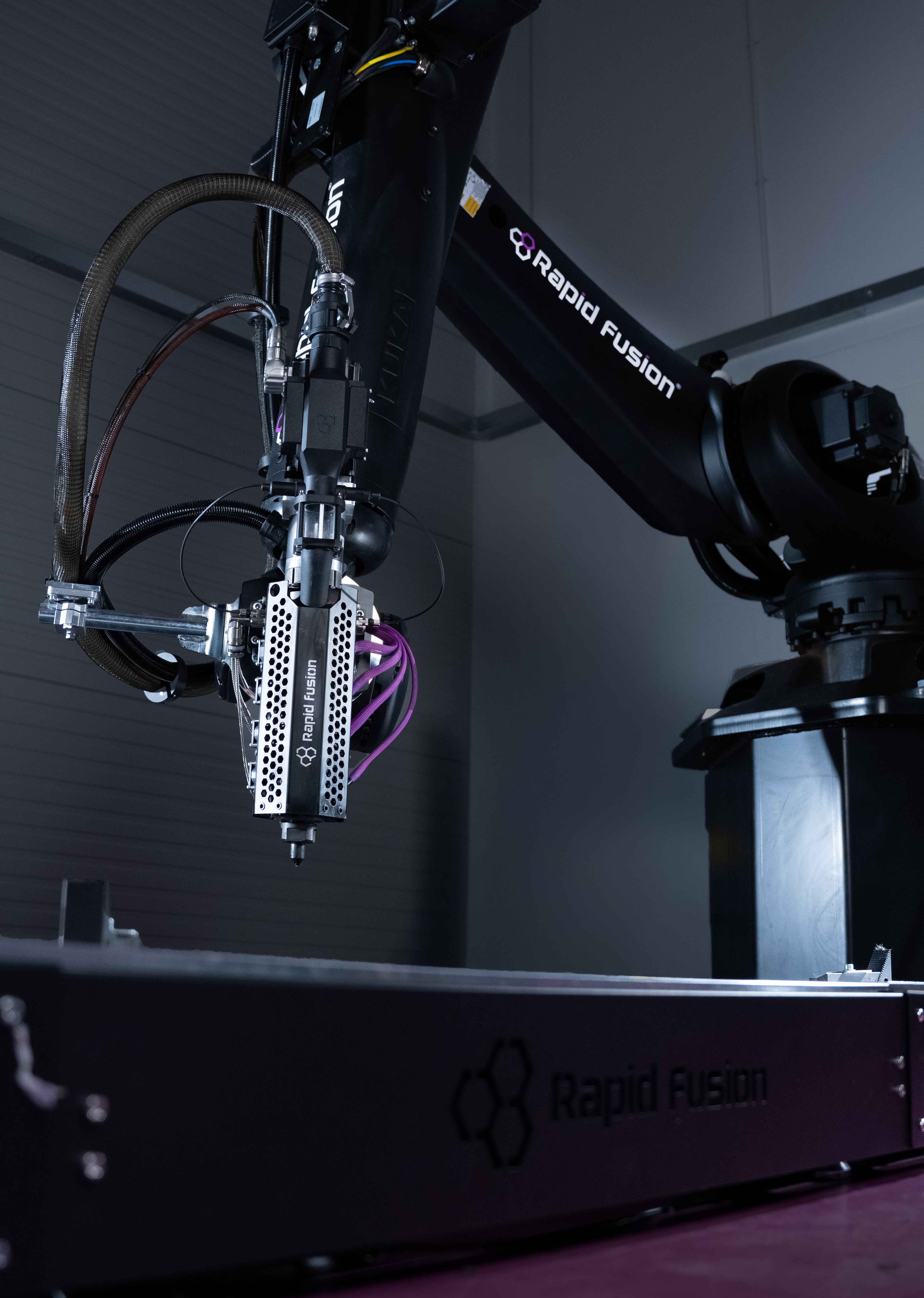
KUKA KR 120 R3900-2 K 1 Robot
The KR 120 R3900-2 K is the robot selected for use with Apollo, chosen for its balance of speed, strength, and precision in large-format manufacturing setups.
With a rated payload of 120 kg, it’s built to maintain excellent dynamic performance, even during heavy-duty tasks, ensuring stable, reliable operation.
Ideal for additive manufacturing, subtractive milling, and other digital workflows, making it a flexible tool for a range of industrial applications.
Engineered to support high-speed, high-precision work, it helps deliver consistent part quality and efficient cycle times across projects.
Designed with the future in mind, this robot helps future-proof your production setup, supporting ongoing growth and adaptability in advanced manufacturing.
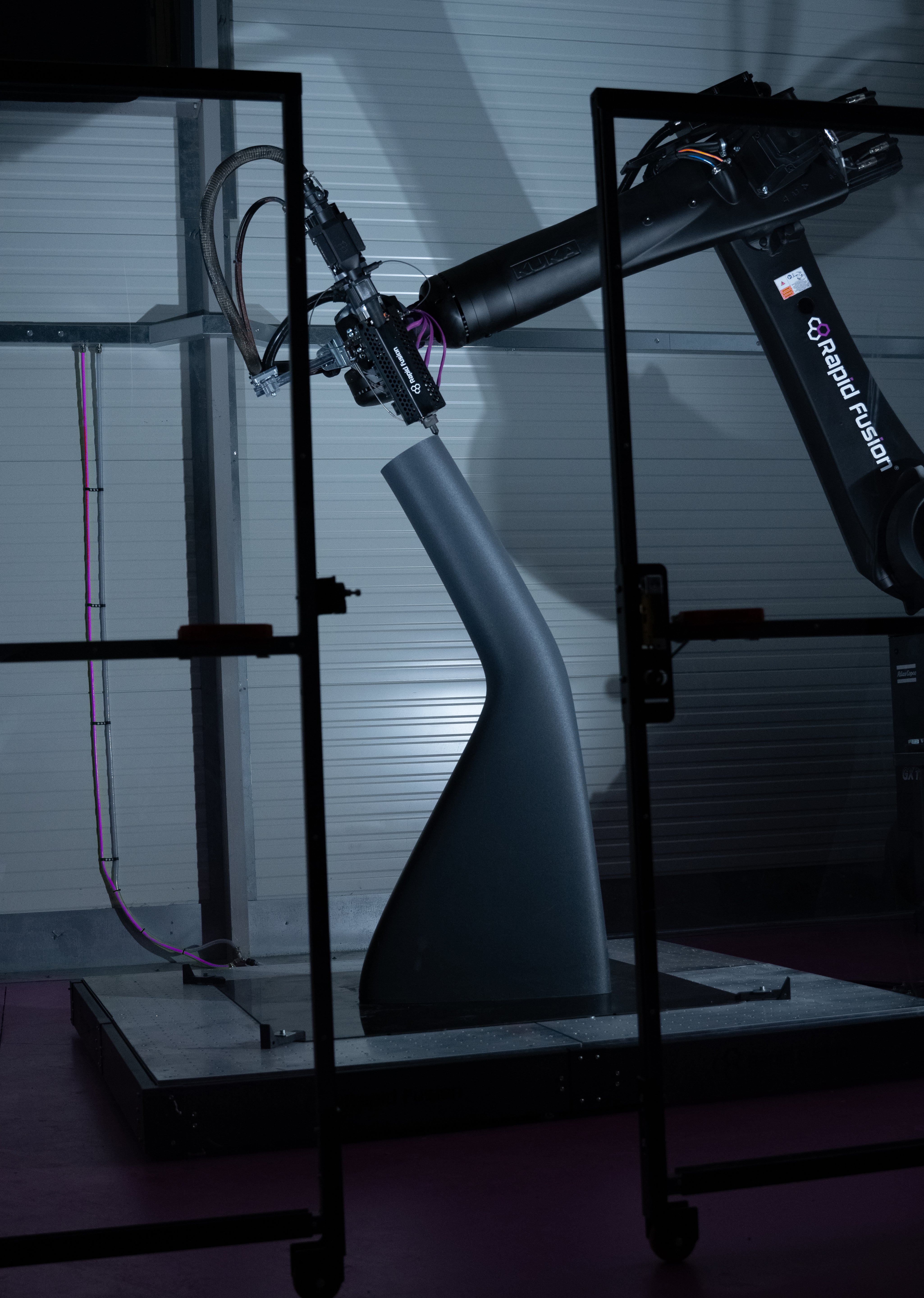
Enclosure
The Safety Cell is built around three core principles: flexibility, straightforward installation, and full compliance with safety regulations. It's a smart, well-designed system that provides reliable protection in a wide range of industrial environments.
With a wide selection of standard components and clever accessories, the system can be adapted to suit almost any requirement. You can also combine different setups to create a fully customised solution.
The Safety Cell is designed to be quick to install, keeping downtime to a minimum. Its user-friendly setup means you can get up and running with less effort and fewer delays.
Fully compliant with all current machinery directives and safety standards, the system can also be extended with options like cable trays and impact protection for added peace of mind.
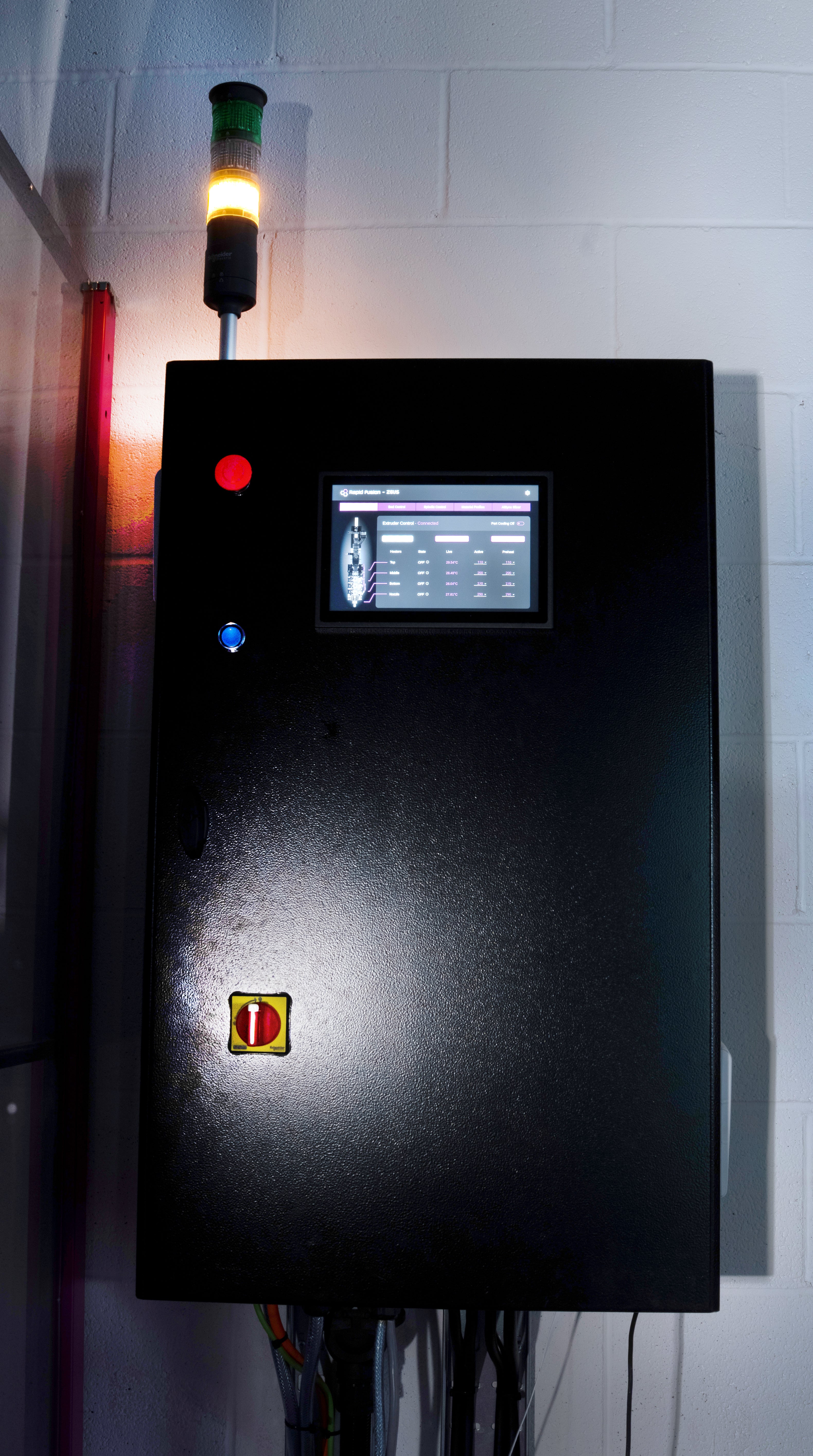
Rapid Fusion Epicurus Controller Pro
The Rapid Fusion Control Console Pro is an open-source solution built to power large-format additive manufacturing. It integrates smoothly with systems like PE320, Dyze Design Pulsar, CEAD, REV3RD, and MD for a fully connected workflow.
Get direct control over servo drives and machine movements when connected to a robot or CNC, delivering precise, responsive performance for demanding print jobs.
Adjust extruders, bed heaters, and part cooling with precision. Pre-set heating zones and in-slice temperature control help maintain consistency across complex prints.
With a licensed AiSync PRO setup, the console streams real-time instructions to your robot or CNC, supporting fleet management, automated error detection, and full process coordination.
A 10.1" touchscreen, integrated safety features, and maintenance key make operation safe, simple, and efficient—even in busy production environments.
Aibuild
Apollo integrates seamlessly with Aibuild, an advanced software platform for robotic additive manufacturing.
Adaxis
Apollo is also fully compatible with Adaxis, a robust tool for programming and controlling robotic additive processes.

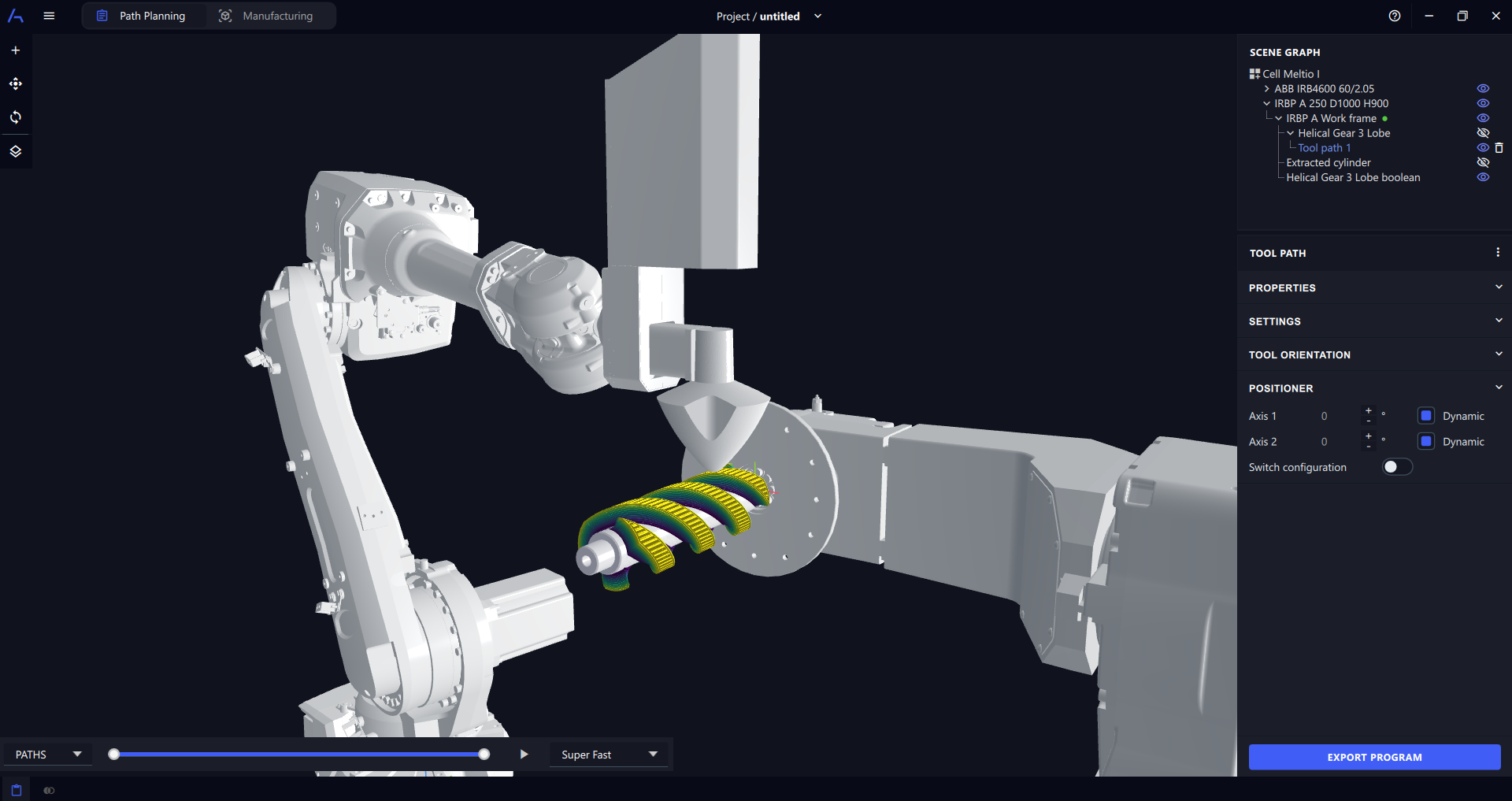
Download Our Apollo Brochure